Bass Pedalboard Build 2020
- Phill Court
- Aug 10, 2020
- 11 min read
Updated: Jan 15, 2022
At the start of lockdown (March 2020) I was constantly watching a YouTube channel called Vertex Effects and his custom pedalboard builds for many of the worlds most accomplished musicians.
I was quite happy with my pedalboard at the time, but it lacked the reliability & ease of use that many of my peers had! I was constantly building up & tearing it down depending on the show('s) I was performing in.
So I invested in some new hardware & accessories & started my build.
Just a quick note! I didn't purchase any new pedals as I'm very happy with the sounds & tones I can make & use for my bass in many different situations & scenarios.
Old Pedalboard
Heres my original "full" pedalboard that I started with.
Essentially a Pedaltrain Classic Jr with an MXR DC brick power supply & generic patch cables.
All in all, a pretty good pedalboard, but quite noisy, bulky & from tearing it down & building up somewhat unreliable!
After watching all of Mason's videos, livestreams & reading his articles I wanted to start from the ground up & use top quality materials & techniques.
Components In Full
The Board
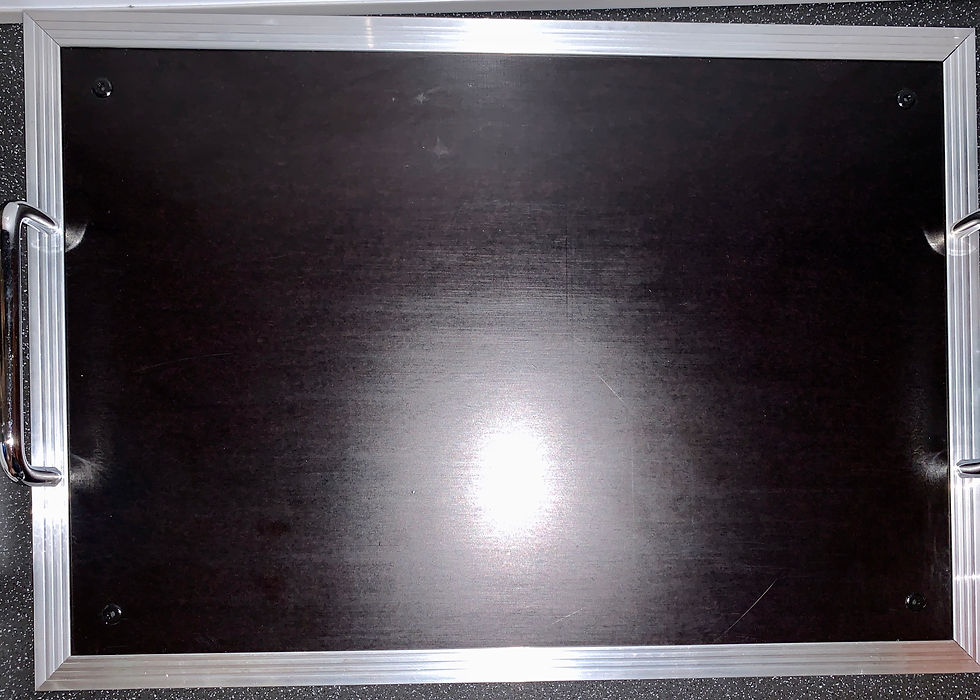
The flat pedalboard was different to my angled Pedaltrain, but thats sort of the way the industry is moving, plus it looks so cool! So I contacted Swanflight who made my custom bass rig flightcase. I emailed them the internal dimensions of my old Pedaltrain flight case, so I could re use it & save some money!
Overall an excellent quality of board & very sturdy & I know that it will hold up well from using Swanflight's products before.
Dimensions 460mm x 320mm
Purchased from SwanFlight
Price £70
The Power Supply

My MXR DC Brick was good, but quite noisy & years on the road have taken it's toll! After researching the best power supplies available I went with the best! The Strymon Zuma Power Supply. So powerful & quiet & a good looking piece of kit! With so many switching & extension options too!
Purchased from GAK
Price £229
I also purchased some extra Strymon 18" DC Power cables to help with tidying the overall power loom for the pedalboard.
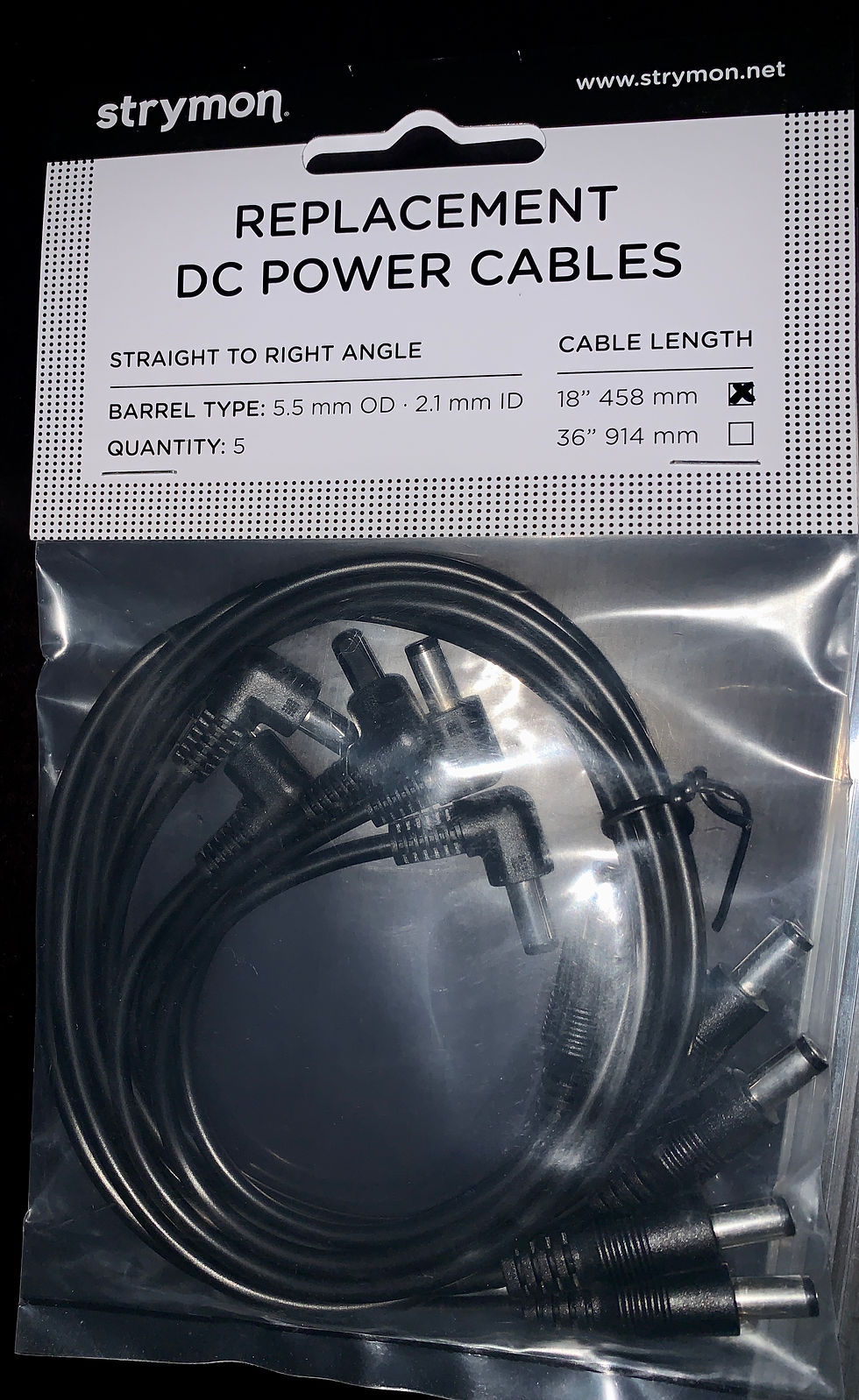
Purchased from Hot Rox UK
Price £22
Pedal Tier
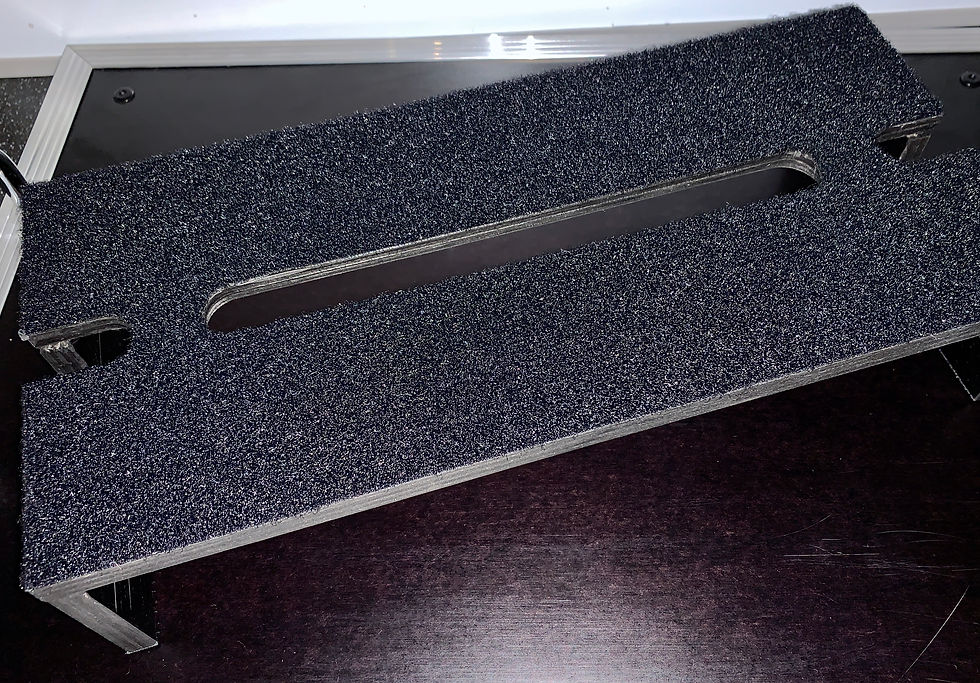
Because of the flat board design I couldn't hide my power supply underneath so like many of Mason's builds I required a pedal tier/bridge to allow me to hide my PSU & mount pedals on top. It took so long to find a UK supplier, I thought I'd never find one! I contacted Custom Pedal Boards, on the recommendation of Matt Downer, an outstanding bass player & pedalboard genius. A big shoutout to him for all the help & answering all my annoying questions!
After a few questions I ordered the CPB Universal Tier (ultra small) which is a sturdy & such a great product & idea.
Purchased from Custom Pedal Boards
Price £59.27
Patch Box

From my research I found it is best not to go straight into & out of pedals due to buffering & pedal wear etc. So I contacted Bright Onion Pedals & ordered the 2 Gang Patchbox to overcome this. Even for the sake of keeping a clean stage area this is well worth it!
With this patchbox it just cleans everything up (cable wise) & adds a great input & output stage separate from my pedals!
Purchased from Bright Onion Pedals
Price £24
Pedal Switcher
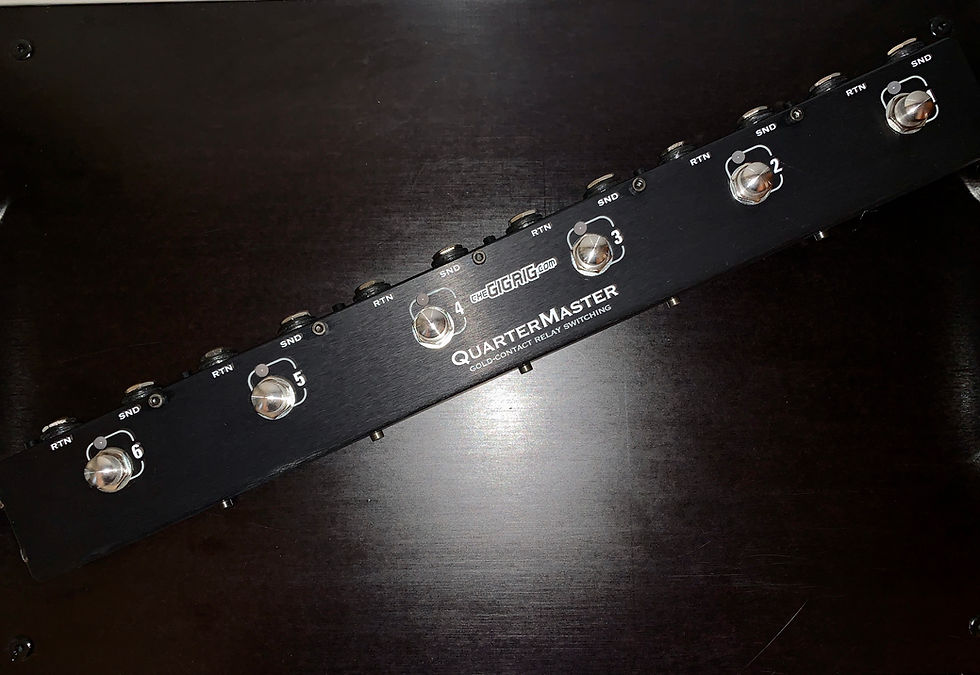
Do I need a switcher? That was the question! although my power supply was the main cause of noise, my pedals with locking latches & the obvious problem of having my signal running through all of the pedals all of the time made the decision a lot easier to make!
Looking at my pedals & watching a few videos, I chose The GigRig QuarterMaster QMX-6 Pedal Switcher.
Reviews were great & the videos from GigRig sold it to me. Although I don't use hundreds of pedals, the switcher makes sure my signal is clean & with the quiet activation of each pedal it makes everything 100% easier to work with.
Purchased from Andertons
Price £199
Patch Cables
I was 50/50 about using soldered or solder-less patch cables. I knew I needed good quality cables that I could cut to the required lengths. My soldering skills aren't the greatest (I know it's down to practice) but due to efficiency & time, plus excellent reviews I went with the PedalPatch medium solder-less kit which had plenty of cable (5m) plus 16 low-profile 1/4" connectors
With the use of my switcher & patchbox I required 12 extra low-profile 1/4" Connectors.
The cable is quite thin compared to most patch cables, which aids in manipulating the cables around obstacles. Also the 1\4" connectors allow them to be either right angled or straight which is so cool! Which I used to its full extent!
Purchased from PedalPatch
Medium Solder-less Kit
£59.99
12 Low-Profile 1/4" Connectors
£47.88
3M Dual Lock Hook & Loop

The only choice really! I used the full size rolls & the smaller ones to help stop waste when mounting smaller pedals etc.
Purchased from Amazon
Price £7.82
3M Cable Harnesses & Various Sized Cable Ties
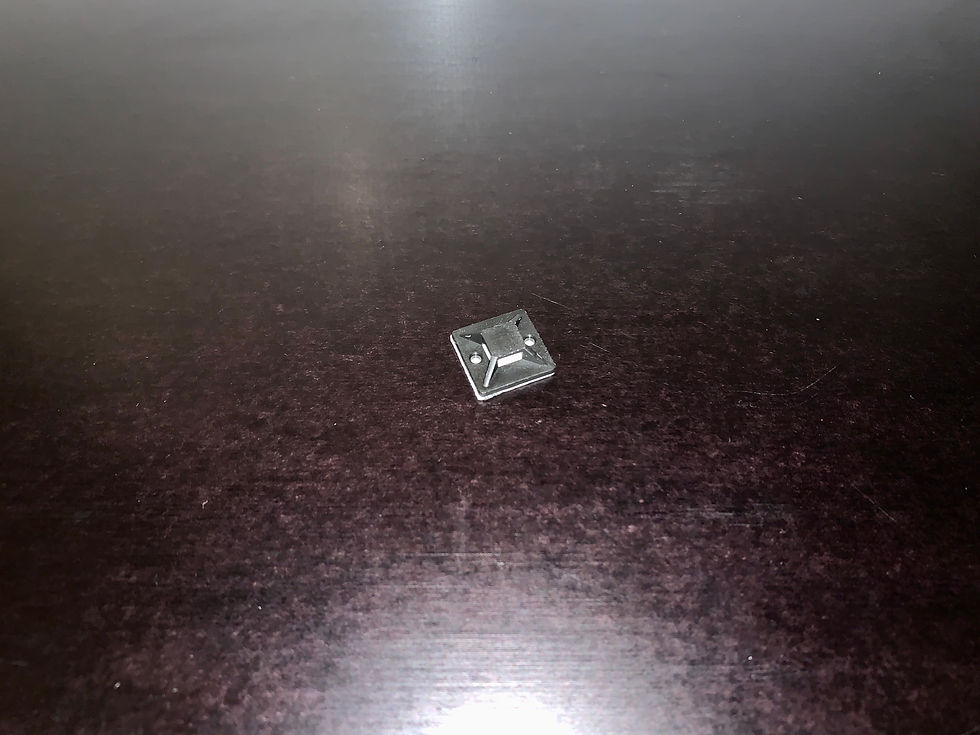
Because of the style of board (no cable routing underneath) I needed a solid solution to keep everything neat, tidy & most importantly, accessible!!
I used these, along with various sized cable ties to anchor DC & audio cables throughout the pedalboard especially the power loom connected to the PSU (a lot of harnesses & cable ties) I made sure to leave a comfortable amount of slack, so nothing was taught, but everything was still tidy & clean looking!
Purchased from Amazon
Price £11.75 (I had plenty of cable ties as most musicians do!)
Brother Label Maker, White on Clear Tape & Duracell AAA Batteries

For my build I wanted everything to be clearly labelled & marked up for ease of building, maintenance & use.
I labeled each pedal with its type i.e. Octave, Delay etc. & also what loop they were connected to in regards to the switcher. I also labelled the PSU with the corresponding pedal each output is powering.
Also, I labeled the function of each loop 1-6 on the switcher, so I know exactly what I'm turning on & off.
Purchased from Tool Station
£23 Label Maker
£6.50 AAA Batteries
£24.59 White on Clear Label Tape
Purchased from Brother
WD40 Contact Cleaner & Black Electrical Tape
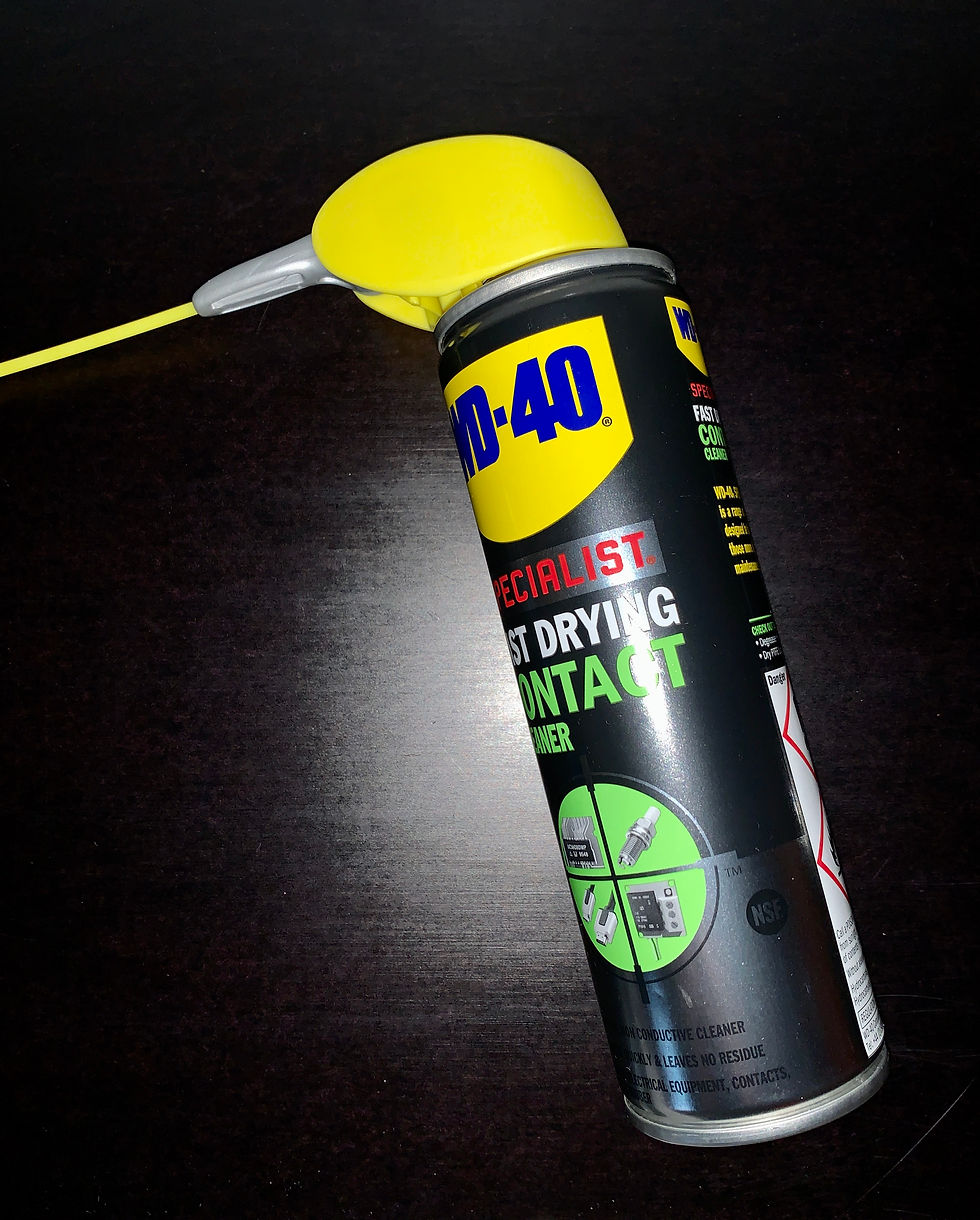
Before the build & on recommendation I cleaned all the inputs & outputs of my pedals with this & also taped up the battery connectors in each pedal to stop any interference or shorting occurring.
Purchased from Tool Station
£4 WD40 Contact Cleaner
£0.20 Electrical Tape
StageTrix Pedal Setting Saver Pen

I already had this StageTrix pen & used to use it quite often to mark pedal settings on the fly & mark equipment.
I decided to mark the setting knobs on the pedals for ease of use on dark stages as it glows in the dark. Also its looks cool as hell!
Purchased from A Strings
£4
The only other tools/equipment used I already owned or had borrowed. Including cleaning solutions, Sharpies, Cable Ties etc.
The Build
Here I have provided some time-lapse's showing most of the build in the various stages.
Firstly I needed a plan to see how many cables needed to be made/purchased & 1/4' connectors. This plan is not to scale or design, but it helped me visualise a game-plan.

Plan Of Action
Secondly I needed to work out what pedals I would use. Space is limited, but I knew I had plenty of room to use the existing pedals.
I used my trusty notebook from Charlie!
To note the following -
6 Loops
9 Power Outputs from the PSU
14 1/4" Cables
IN/OUT & RTN/SND (from patchbox)
Pedal Maintenance
I undertook maintenances of my existing pedals, making sure they were all working, clean & taped up any battery connectors.

Pedal Placement & Initial Power Cable Plan
Next I provisionally placed my pedals, PSU & Hardware. I placed the 1\4" connectors in the pedals & switcher to make sure the room was sufficient between all of the pedals.
I also wrote down rough lengths for the DC cables to gauge an initial idea of cable routing.
Hardware & Pedal Mounting
I attached the PSU, Switcher, Pedal Tier & Patchbox with the Dual Lock. I think that this was the point where I could see my plan coming together!
I made sure there was enough space between all of the pedals & switcher, making sure there was enough room for cable harnesses & both audio & power cables.
DC Power Cable Routing
This was probably the most difficult, but most satisfying part of the build. I placed all the pedals in place & laid out each power cable towards the PSU. This is where having the removable pedal tier came in very handy!
I tied the cables into different looms depending on the location, direction & routing from each pedal.
Using the cable harnesses & ties. I secured the cables in strategic position around the pedalboard & also on the pedal tier. With no cable distortion, awkward angles & a full power test I was extremely happy with the clean look & easy maintenance option available.
I also labeled each output on the PSU with the loop which corresponds with the loop number & pedal it is powering.
Label Making
I like order & I like having everything cleanly labelled & set out.
This was probably the most relaxing part of the build.
I labeled each pedal with its function i.e. OCT, TUNER etc & the loop it corresponds with on the switcher i.e. LOOP 1, LOOP 2 etc.
I used white on clear tape to give it a nice sharp & easy to read look. I used a sharpie to colour in some of the GigRig loo so my label could be read properly.
1/4" Audio Cable Making & Routing
I completed this step outside near my pool in the lovely Welsh sunshine. Unfortunately the quality of the time-lapse for this step was unusable (but watch this space)
I cut and set each cable individually & used a similar loom system for groups of pedals depending on location & direction of cables to & from the switcher & pedals respectively.
I again used the cable harness tie downs & cable ties (also the existing ones from the DC cables) to anchor these down. I absolutely love how short some of the 1\4" is, mainly going from the switcher to a pedal!
Making sure there was enough slack & no distortion, weird angles or pulling on the cables I fastened them down. I made sure there. was space between DC & 1/4" and no parallel lines as best I can to keep any interference to a minimum.
Final Tests & Troubleshooting
I plugged in & powered the PSU then the 1\4" in the send & return & had an awful buzz & convection issue.
I isolated the problem (using the loop labels & individual looms) and made sure the connections on two cables were secure & we were back in business!
I ran the pedalboard for a few hours monitoring any sound or heat issues with none presenting.
The Pedals & My Uses For Them
Here we have the pedals in question! Just brief rundown of what I use them for & if I layer them with any others.
MXR Bass Compressor
Purchased from A Strings
This is an "always on" pedal for nearly every occasion. Thats why it isn't in a loop & is the first pedal contact even before the switcher. I normally run it quite moderately but can really get some rest 80's squashed sounding bass through it.
MXR Bass Octave Deluxe
Purchased From A Strings
Listed as OCT 1 & Loop number one. It is my go-to octave. Mainly used for the sub bass sounds or my "Pino" moments. Great to layer with the dry bass signal or with added delay for some awesome synth parts.
Electro Harmonix Nano Pog
Purchased from Andertons
My go to for octave up sounds, for solo bass only performances or add in the dry, octave up & octave down for my "default" bass solo sound ala Bill Banwell.
Adding in a reverb like delay provides my go to solo sound with Jazz Quintet The Bakery
Digitech Bass Synth Wah Bass Envelope Filter
Purchased from A Strings
Originally a very inexpensive pedal, now discontinued & widely sought after!
Main use is a synth tone if I'm not running my Moog or other bass synth.
Used quite a lot with the Beyoncé tribute Reyoncé mainly for the track - Single Ladies.
A very useful & usable auto wah! which saves space from having a full sized wah pedal. Plus I can get some really cool Herbie Hancock tones too.
Good to layer with some delay or distortion for a sharper/dirtier synth sound
Tone City Tape Delay
Purchased From Andertons
Not really used as a delay very often, normally a kind of reverb. I sometimes turn everything up & move the rate knob to get a cool rewound tape sound. normally used for my Jazz soloing or chordal accompaniment. Work well with the octaves.
MXR Bass DI +
Purchased from A Strings
The heavy pedal! with three! distinct uses.
Firstly as a preamp/EQ that I use probably more on modern/pop gigs to get a "hifi" bass sound.
Secondly as a distortion pedal to add a crunch or full on distortion for rockier things.
Thirdly as a separate DI which is used if I'm not using an amp or other external DI's or as an emergency spare.
Distortion works well with the synth & octave pedals usually.
Boss TU3 Chromatic Tuner
Purchased from A Strings
The gold industry standard! set up with o return on the switcher as to use as a muting/kill switch system along with its tuner function. You cant go wrong!
Regrets, Changes & Future Options?
After the build & testing/use theres only a few things I believe I would change, add or have tackled differently.
The possibility of using soldered cables. These cables are very sturdy & will hold up. I may switch them to soldered ones in the future or other builds.
The use of custom DC power cables. I think that using or trimming existing DC cables would make the routing & loom a lot easier overall.
I believe I would tackle the issue of routing the cables differently & possibly easier by choosing a slightly larger board.
I may swap out the Boss TU3 for the TU3S as I don't need the foot-switch & I could flip the display to make it a little bit easier to read on stage.
I still need to find a replacement know for the MXR Bass Compressor ratio settings.
I may look at getting a knob cover for the delay pedal to ease the use while performing live, to gain the "rewound tape" effect.
A new power cable (longer & better shielded) would be a good addition.
I may purchase a new custom flight case for the board, instead of re using my original Pedaltrain one.
Final Thoughts
Overall I am over the moon with what I have achieved & the professional look, fit, finish & use of this bass pedalboard. It will be my main board for the foreseeable future. I'm so happy & the quality audio wise, is second to none!
Im currently thinking about venturing into the professional world of custom pedalboard building depending on the interest.
I honestly think this project has helped me cope during the extended lockdown here in Wales & I'm very thankful to be in a position where I could put this together.
Final cost without pedals or delivery charges or my own labour - £804.68
Heres a playthrough of my pedalboard. I'm using a Fender American Deluxe Jazz Bass V with round wound strings straight into Logic Pro X with no audio effects or editing.
A massive thank you to the following people & companies for offering advice, help, products & expertise (including links)
& everybody else who had an input in this amazing project!
Phill.
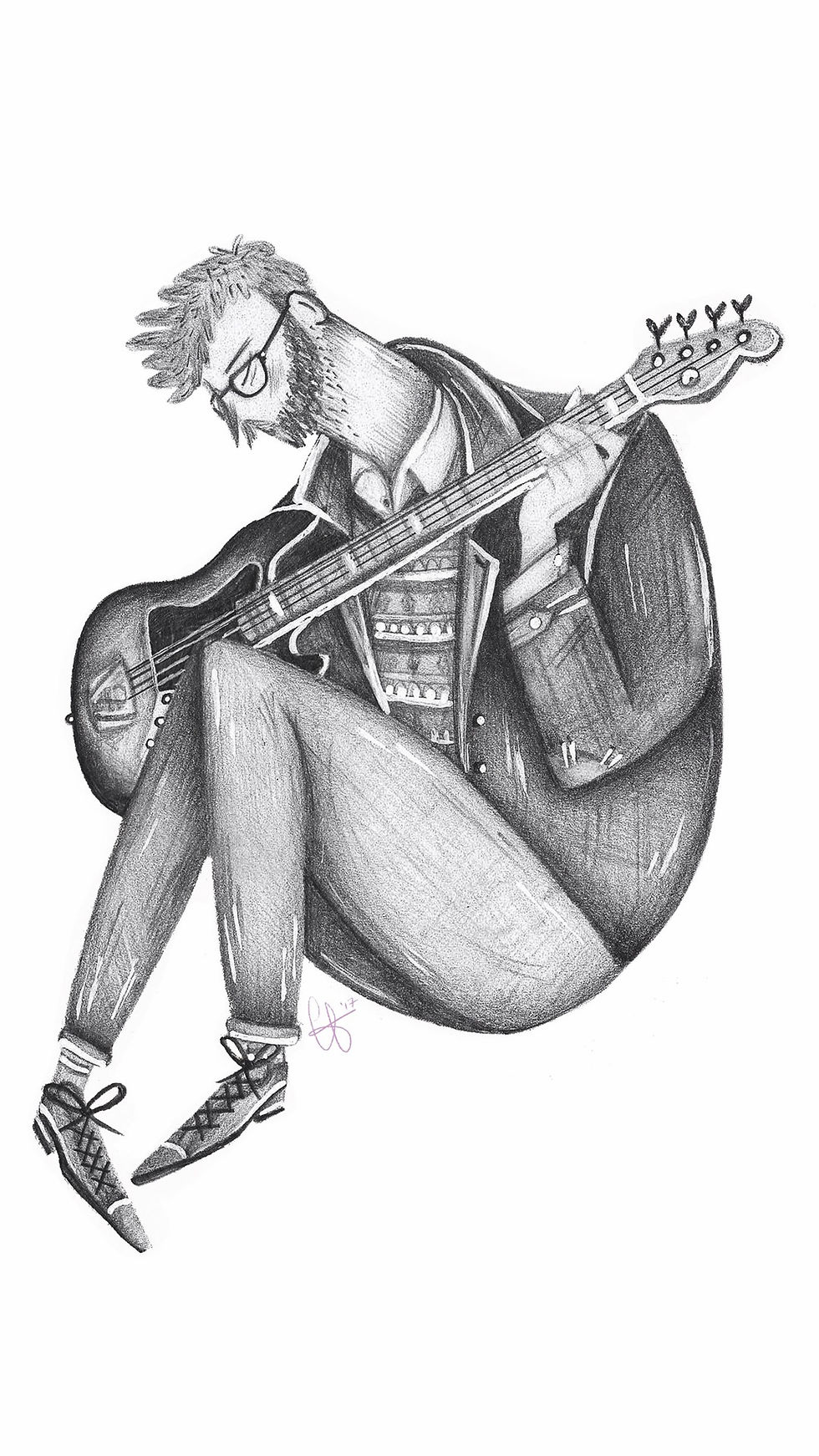
My Links
email: info@phillcourtmusic.com
댓글